Understanding the Process and Production of PVC Thermal Insulation Bags
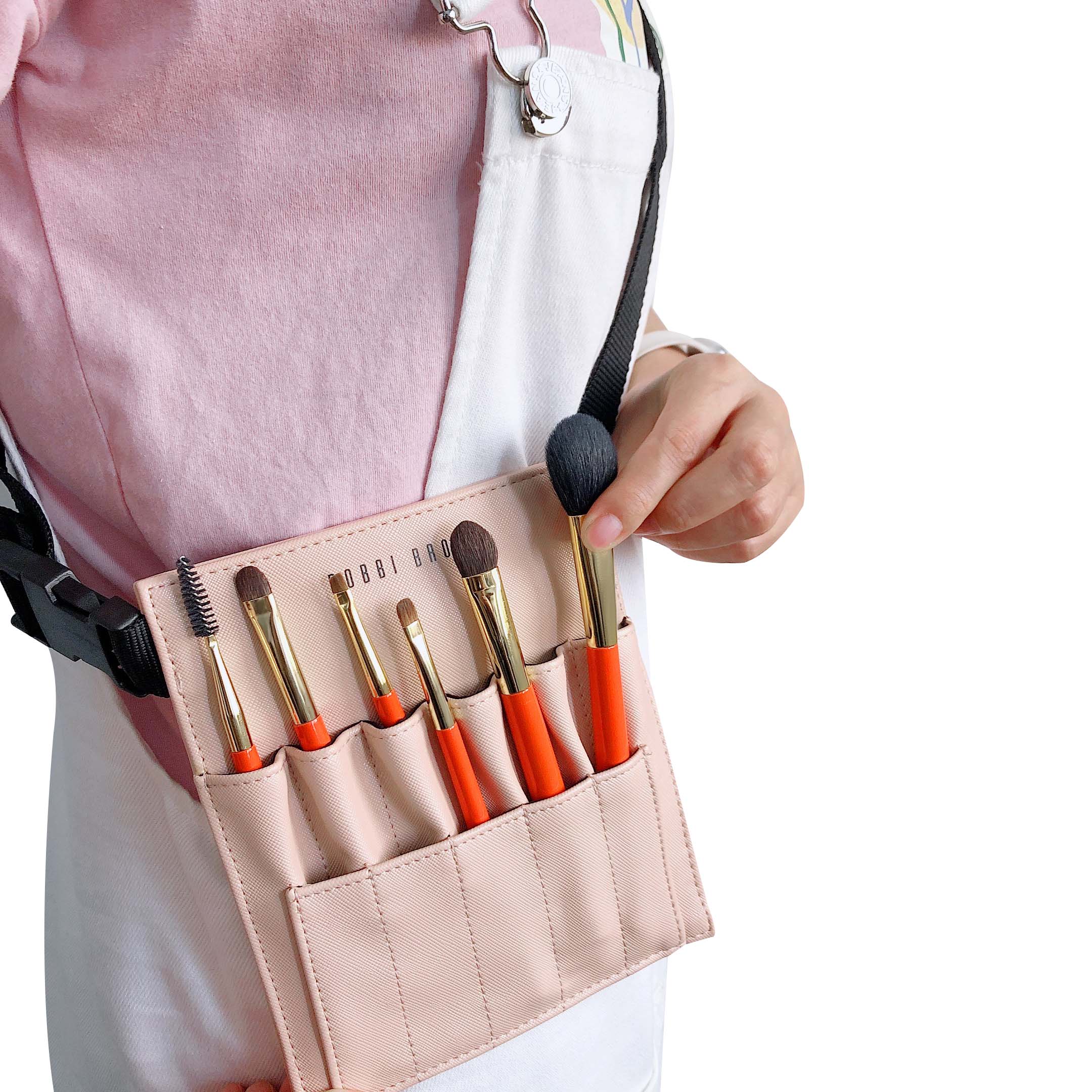
When it comes to maintaining the desired temperature of perishable items, PVC thermal insulation bags have become an essential tool in various industries. These bags are designed to keep the contents cool or warm, making them ideal for transporting food, medicine, and other temperature-sensitive products. In this article, we will explore the production process and steps involved in manufacturing PVC thermal insulation bags.
1. Selection of High-Quality PVC Material
The first step in the production process of PVC thermal insulation bags is to select the right PVC material. High-quality PVC with excellent thermal insulation properties is crucial to ensure the effectiveness and durability of the bags. The chosen material should have low thermal conductivity and be resistant to wear and tear.
Manufacturers carefully choose PVC materials that meet these requirements to ensure the bags' insulation capabilities and durability in extreme temperature conditions.
2. Designing and Cutting the PVC Material
Once the PVC material is selected, the next step involves designing the bag according to the desired specifications. The design includes determining the bag's shape, size, and compartments based on the intended purpose.
After the design is finalized, the PVC material is cut into the required dimensions. Advanced cutting techniques, such as die cutting or laser cutting, ensure precision and accuracy in producing consistently sized PVC parts for the bags.
3. Sewing and Assembling the Insulation Bags
The cut PVC parts are then assembled and sewn together to form the PVC thermal insulation bags. Using high-quality sewing machines, skilled workers create sturdy seams and secure the edges to prevent any leakage or damage to the insulation.
During the assembly process, additional features like handles, zippers, or velcro closures may be incorporated, depending on the bag's design and purpose.
4. Quality Control and Final Inspection
Before the PVC thermal insulation bags can leave the production facility, they undergo meticulous quality control procedures to ensure they meet the required standards.
Trained technicians conduct thorough inspections to check for any defects, such as faulty stitching, weak seals, or substandard insulation. Bags that pass the quality control measures are then properly packed and prepared for shipping.
Conclusion
The production process of PVC thermal insulation bags involves the careful selection of high-quality PVC material, precise cutting, and the skilled assembly of the bags. These bags play a vital role in maintaining the desired temperature of perishable items during transportation and storage. Understanding the production process gives us insight into the dedication and craftsmanship that goes into creating these essential tools for industries worldwide.
Tags: